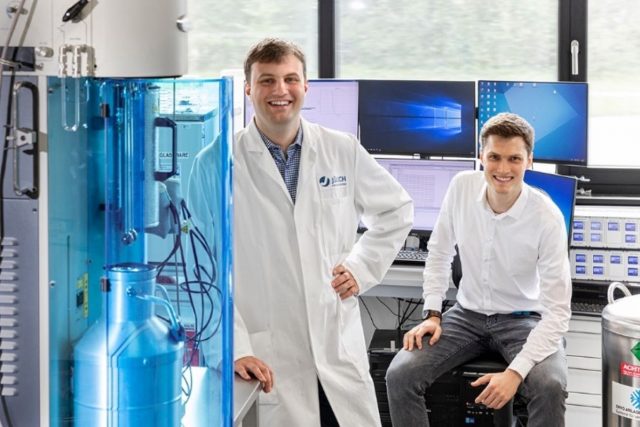
Ansgar Kretzschmar steht vor einem Labortisch und deutet auf den durchsichtigen Würfel darauf, etwa so groß wie eine Waschmaschine: „Der besteht aus Acrylglas. Eine reine Sicherheitsvorkehrung. Darunter stellen wir unsere Fasermatten her bei einer Hochspannung von 25.000 Volt.“ Dieses Vlies aus feinsten Kunststofffäden könnte dabei helfen, eines der größten Probleme unserer Zeit anzugehen: den menschengemachten Klimawandel.
Denn um die Erderwärmung auf 1,5 Grad Celsius zu begrenzen, wie im Pariser Klimaabkommen gefordert, wird es auch nötig sein, das Treibhausgas Kohlendioxid wieder zum Teil aus der Atmosphäre zu entfernen. Und dazu bedarf es Materialien, die CO2 in Industrieabgasen selektiv binden. Solche Kohlendioxidfänger entwickeln die Doktoranden Ansgar Kretzschmar und Victor Selmert am Institut für Energie- und Klimaforschung (IEK-9).
„Es ist natürlich sinnvoll, das Gas dort abzufangen, wo es in großen Mengen anfällt: in Biogasanlagen, bei der Müllverbrennung und in Zementwerken. Das sind drei bedeutende Kohlendioxidquellen, die sich auch nach der Energiewende nicht vermeiden lassen werden“, sagt Victor Selmert.
Das CO2 könnte abgetrennt und unter Einsatz von regenerativem Strom wieder in hochwertige Chemikalien umgewandelt werden, wie etwa Methanol, Ameisensäure und andere Plattformchemikalien. Das sind grundlegende Zutaten, die in der Chemie häufig in großen Mengen genutzt werden, um daraus eine breite Palette von Spezialprodukten zu synthetisieren. So entstünde eine Art Kreisprozess für den Kohlenstoff. Die praktische Umsetzung des Konzeptes hält jedoch einige Herausforderungen bereit, erläutert der Forscher: „All diese Gasströme enthalten neben Kohlendioxid auch noch andere Komponenten. Um das CO2 verwerten zu können, muss es möglichst selektiv abgetrennt werden.“
Stickstoff, der Hauptbestandteil der Luft, macht einen großen Anteil an all diesen Gasgemischen aus. Daneben können sie auch mehr oder weniger große Mengen von Wasser enthalten. Und in Biogasanlagen liegt neben CO2 vor allem das begehrte Methan vor, das eigentliche Produkt dieser Anlagen.
Die beiden Forscher aus Jülich suchen nach Materialien, die möglichst nur das Kohlendioxid an sich binden und die übrigen Gase vorüber streichen lassen. Solche CO2-Fänger werden üblicherweise zu Pellets gepresst, die sich das Treibhausgas wie ein Schwamm solange aufsaugen, bis sie voll beladen sind. Dann kann das reine Kohlendioxid wieder abgegeben werden – entweder indem man kurzzeitig die Temperatur erhöht oder den Druck senkt
Verschiedene Materialien bieten sich dafür an, ein jedes mit ganz speziellen Stärken und Schwächen, so Ansgar Kretzschmar: „Eine eierlegende Wollmilchsau gibt es bisher nicht. Häufig verwendet werden hochgeordnete poröse Materialien, wie etwa mineralische Zeolithe oder maßgeschneiderte metallorganische Gerüstverbindungen, die sogenannten MOFs. Beide Substanzklassen binden Kohlendioxid sehr selektiv, geben es aber hinterher nicht gerne ab. Um das Material zu regenerieren, ist also recht viel Energie notwendig. Außerdem können diese Stoffe sehr teuer sein.“
Wesentlich günstiger kommen da CO2-Fänger auf Basis von Kohlenstoff, etwa Aktivkohle. Allerdings saugt das Material auch andere Gase aus dem Abgasstrom auf, worunter die Trennwirkung leidet. „Aktivkohle ist billig, stabil und gut zu regenerieren. Wir versuchen, ihren Hauptnachteil aufzuheben, nämlich ihre geringe Selektivität“, sagt der Forscher.
Hier kommt die Hochspannungs-Apparatur unter dem Acrylglaswürfel ins Spiel. Mit ihr können die beiden Wissenschaftler die Vorstufe ihres CO2-Fängers herstellen. „Das ist eine Elektrospinning-Anlage“, erklärt Ansgar Kretzschmar und deutet auf eine Plastikspritze, die in einer Halterung auf dem Tisch eingespannt ist. „In der Spritze befindet sich ein gelöster Kunststoff, Polyacrylnitril. Die viskose Flüssigkeit drücken wir langsam aus der Kanüle heraus. Dort an der Nadelspitze kann man einen kleinen Tropfen davon sehen, wenn man gute Augen hat.“
Gut fünfzehn Zentimeter davon entfernt dreht sich eine Metalltrommel. „Das ist unser Kollektor. Zwischen ihm und der Kanüle liegt die Hochspannung an. Sie zieht immer ein wenig der Kunststofflösung in Richtung der Metalltrommel. Auf dem Weg dahin verdampft das Lösungsmittel, und es bilden sich feine Kunststofffasern, die auf dem Kollektor allmählich eine dichte, weiße Matte bilden.“
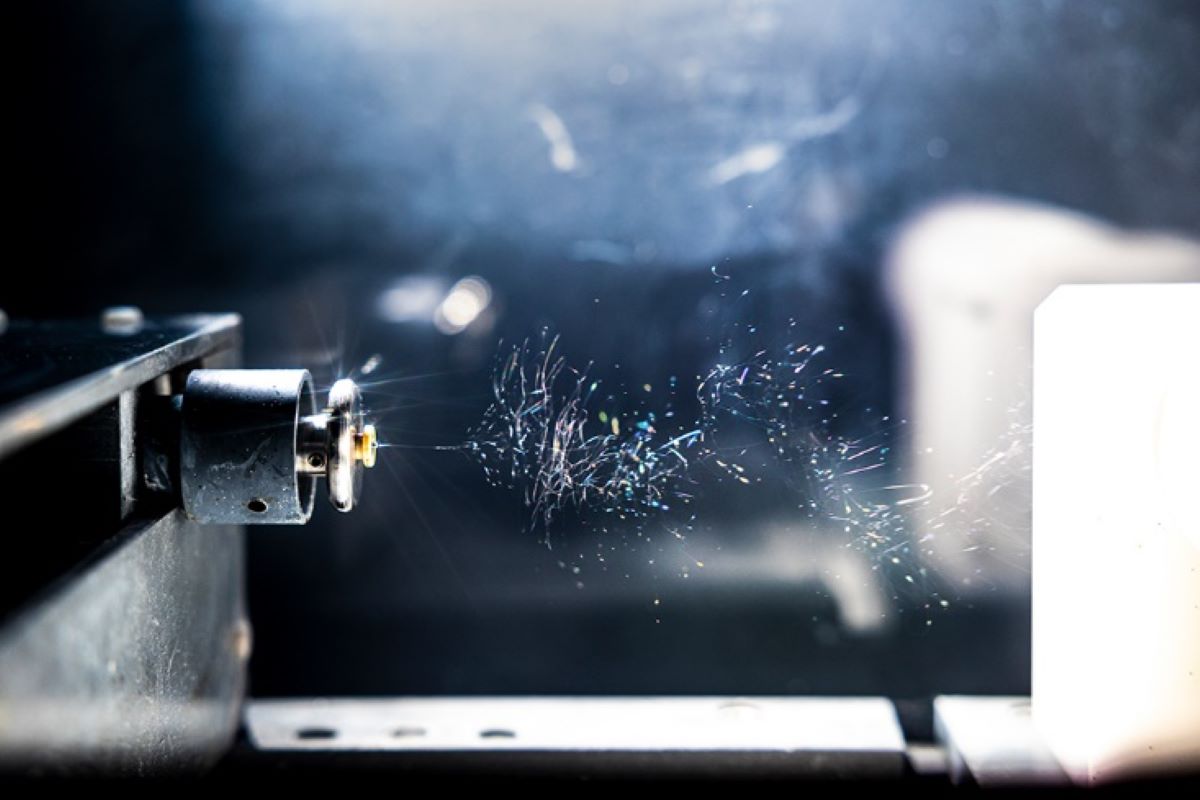
Elektrospinning an sich ist nicht neu. Ein erstes Patent darauf wurde bereits im Jahr 1900 erteilt. Doch zum Herstellen von Textilfasern erwies sich das Verfahren damals als ungeeignet, weil der Durchsatz zu gering war. Wiederentdeckt wurde das Elektrospinning erst vor rund zwanzig Jahren als eine Methode der Nanotechnologie, die inzwischen auch im industriellen Maßstab mit hohem Durchsatz verfügbar ist. Victor Selmert: „Die Polymerfasern in unserer Matte sind extrem dünn, bloß zweihundert Nanometer im Durchmesser. Das ist gut hundertmal dünner als ein menschliches Haar.“ Dadurch besitzen sie eine große Oberfläche, die entscheidend ist für Adsorptionsvorgänge.
Doch bevor die Kunststofffasern CO2 aufsaugen können, müssen sie noch zu Kohlenstoff umgewandelt werden. Dazu werden sie auf 600 bis 1.200 Grad Celsius erhitzt, so dass Stickstoff und Wasserstoff in Form flüchtiger Verbindungen abgespalten werden. Weil der Kunststoff bei diesen Temperaturen an der Luft einfach verbrennen würde, muss diese Umwandlung unter Abwesenheit von Sauerstoff stattfinden. Die Jülicher Forscher führen diese Carbonisierung daher in einer Inertgasatmosphäre durch. So entstehen schließlich hauchfeine Fasern, die zum größten Teil aus Kohlenstoff bestehen.
„Die weiße Fasermatte wird dann schwarz“, sagt Ansgar Kretzschmar und holt aus einer Schublade eine Petrischale mit einer Probe des Materials. „Sie fühlt sich fast wie Papier an, ist aber sehr brüchig.“ In dieser Form eignet sie sich als selektiver CO2-Fänger, der das Treibhausgas aber bei der Regeneration bereitwillig wieder abgibt.
„Wir denken, das liegt an der Oberflächenstruktur der Kohlenstoff-Nanofasern. In Faserrichtung verlaufen dort Furchen. Dort hinein passen die Kohlendioxidmoleküle. Sie setzen sich mit ihren beiden Enden an den Rändern der Furchen fest. Sie sind aber nicht so stark gebunden wie in anderen porösen Materialien. Das heißt, sie lassen sich durch eine Druck- oder Temperaturänderung leicht wieder von der Oberfläche lösen“, sagt Kretzschmar.
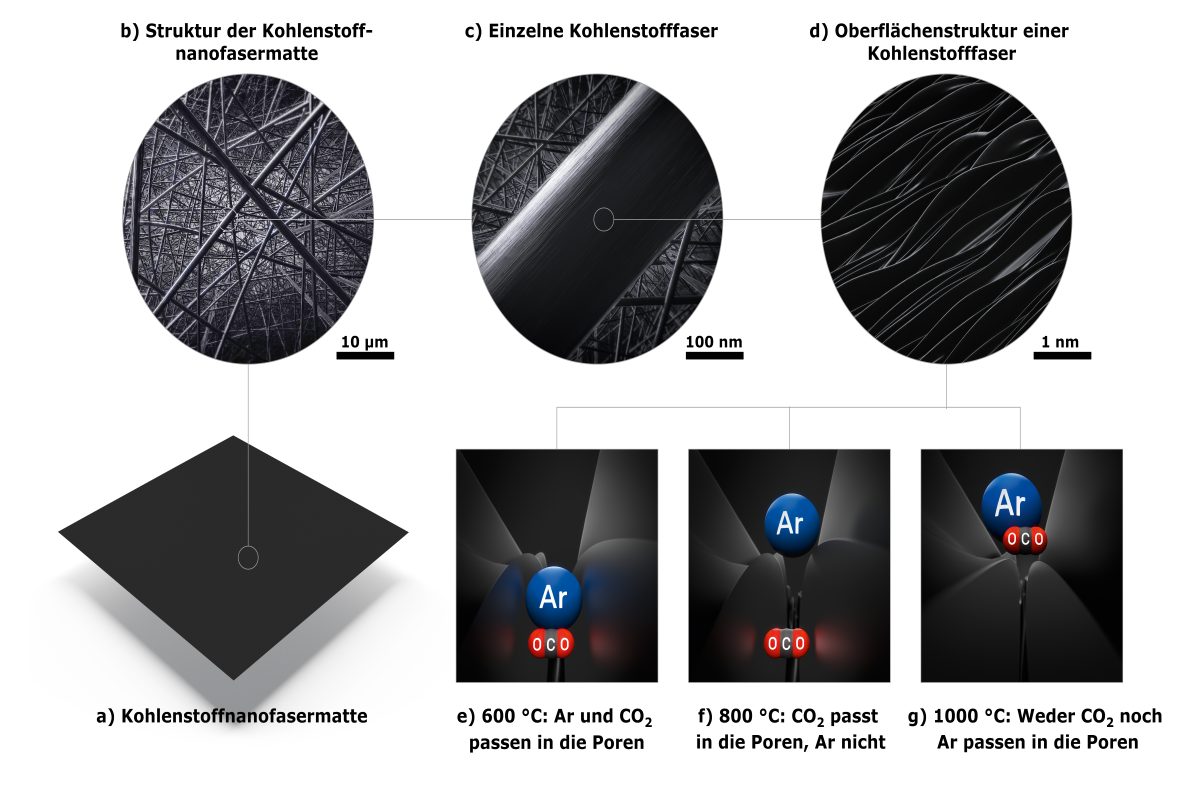
Im Moment denken die Jülicher Forscher darüber nach, das Kohlenstoffmaterial auch dafür zu nutzen, das abgetrennte Kohlendioxid in wertvollere Chemikalien umzuwandeln – mit Hilfe von Elektrolysezellen, in denen die Kohlenstoffmatten, mit einem Katalysator beschichtet, als Elektroden fungieren. Ansgar Kretzschmar: „Abtrennung und Synthese – beide Schritte in einem einzigen Verfahren zu kombinieren, das haben wir uns als Ziel für die Zukunft gesetzt.“